Inside Bruco’s belly!
That’s where a lot of action takes place here at Monolithic.
Plant Manager Donald Garrison puts Airform fabric to the test before any fabric is used to create a Monolithic Airform. Testing allows us to know the fabric’s ability to withstand tension, pressure and seam strength.
The Formula
Fabric tension in a pipe or cylinder (vertical stemwall) is calculated using the formula: Tension = Radius (measured in inches) X Pressure (measured in psi or pounds per square inch).
The formula for a sphere is exactly the same but divided by 2. In other words, the same pressure for the same radius creates twice the tension in the pipe as it does in a sphere.
Tension is the force that tears an Airform as pressure increases. Tension increases for the same pressure as the radius increases. As we usually build portions of a sphere, the actual measurement is the radius of curvature (Rc). For oblate ellipses, we need the Rc for the topmost section of the Airform.
Seam Testing
We seam test the fabric we use. At present, we are generally using reinforced, PVC coated fabric. For homes we use 18oz per square yard fabric, for larger domes we primarily use 28 ounce per square yard and 40 ounce per square yard.
To check an Airform’s ultimate strength, we test it in a hot room of 140 degrees Fahrenheit. We use high heat because we do not want the seam failing on a hot, sunshiny day.
A 28oz fabric seam will hold to 280 pounds per inch ultimate at 140 degrees. The 40oz fabric seam will hold to 380 pounds per inch ultimate at 140 degrees.
We use a five-times safety margin. Tension on the seam should not exceed 56 pounds per inch on the 28oz fabric, nor 76 pounds per inch on the 40oz fabric. We do not want to Fabricate Airforms with a Rc larger than 130 feet for the 28oz fabric, nor 170 feet for the 40oz fabric.
There are several other reasons for not exceeding 170-foot Rc in a smooth dome. A 200-foot diameter dome will have a Rc of 125 for a height of 50 feet – within the margins for the 28oz fabric.
If the height is lowered to 40 feet, the Rc goes to 145 which is too high for the 28oz fabric and must go to the 40oz fabric. Obviously costs will increase both for the Airform and probably the dome.
Note: We first published this article in May 2005.
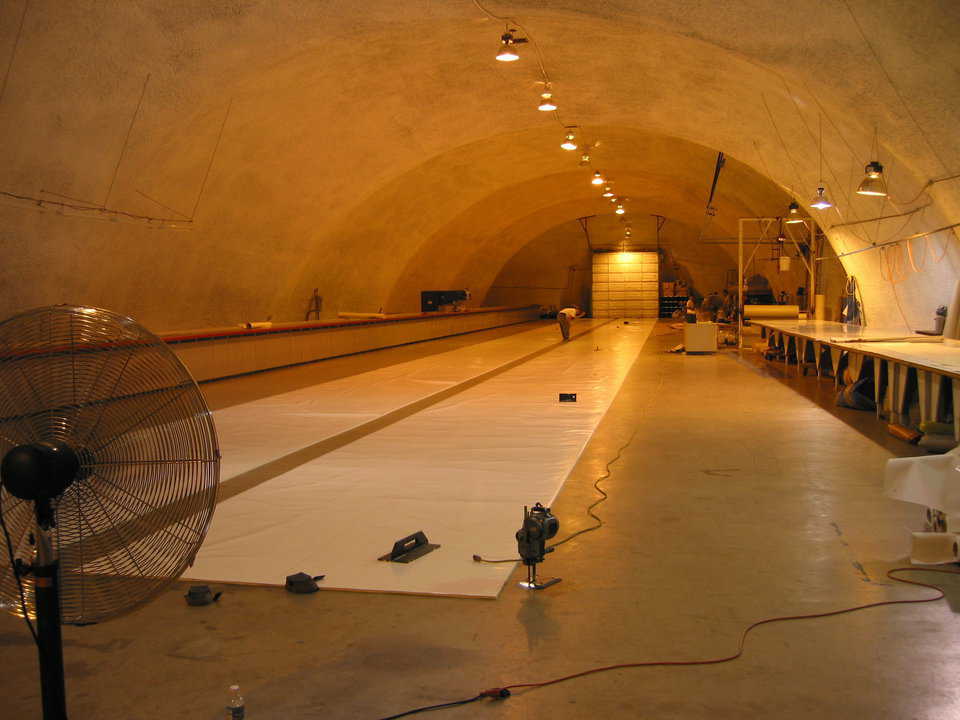
Inside Bruco’s belly — A look down the length of “Bruco” the caterpillar — manufacturing shop for the Airforms. On the floor the fabric is pulled ready for cutting another Airform. (Monolithic Staff)
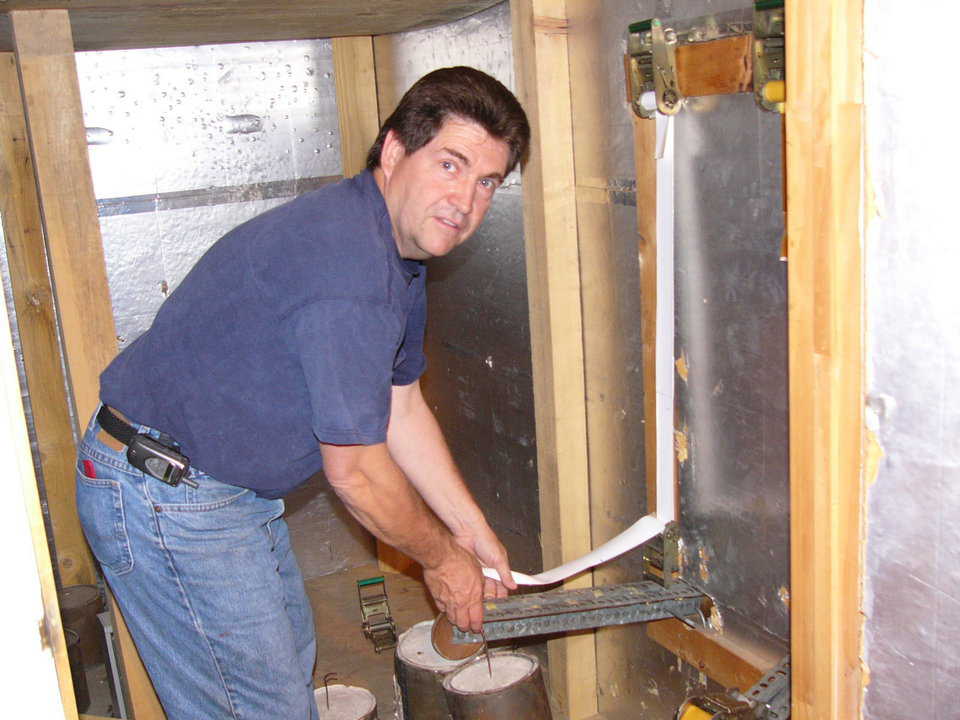
Loading fabric — Don Garrison Superintendent is loading a strip of fabric in the test blocks. Note this is done by actual weights rather than springs. (Monolithic Staff)
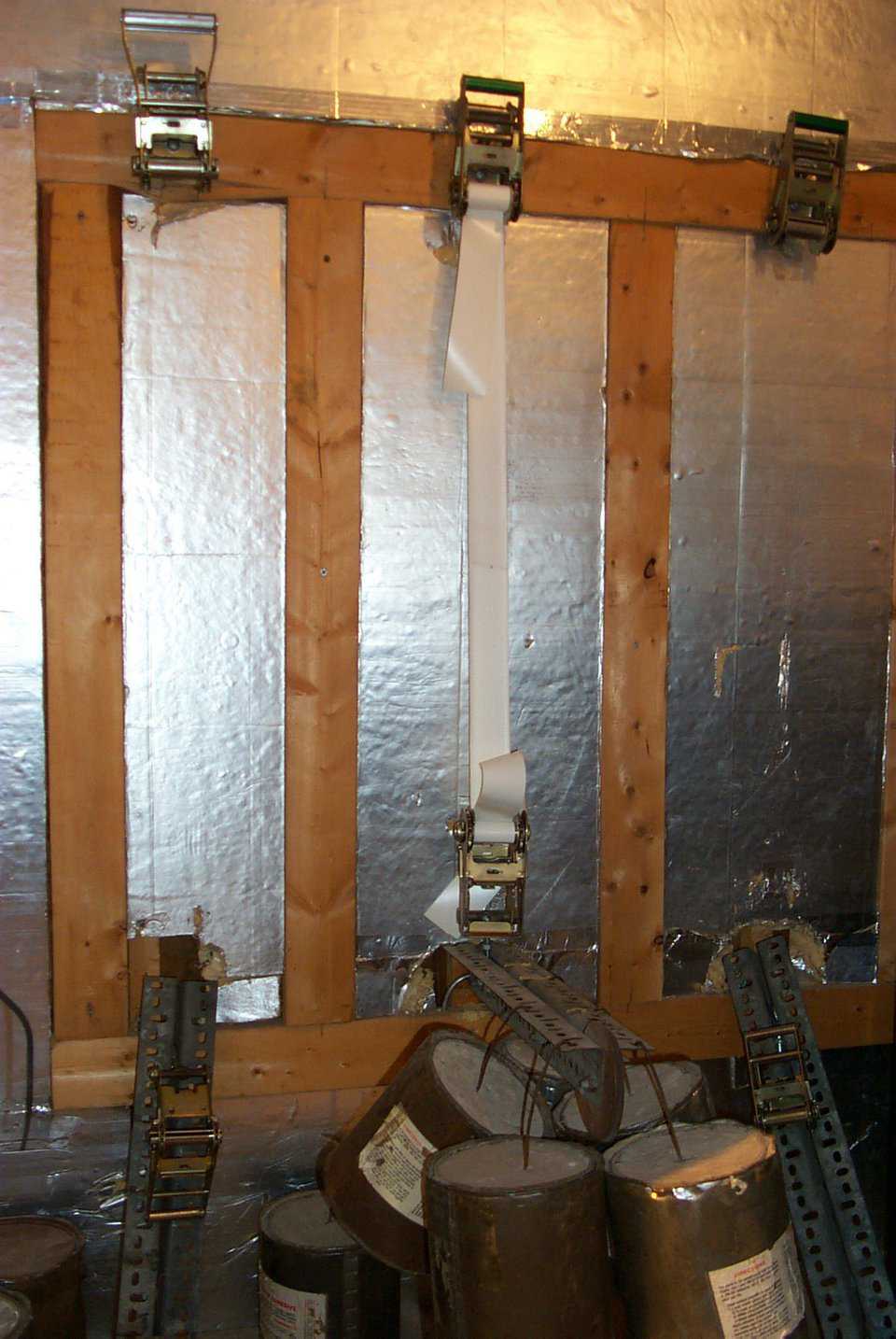
Test chamber — Inside look of the heated test chamber for testing stretch and failure of fabrics. Note the fabric is put under tension in this 140 degree F chamber for 24 hours. (Monolithic Staff)