Measuring Seam Strength in a Monolithic Airform
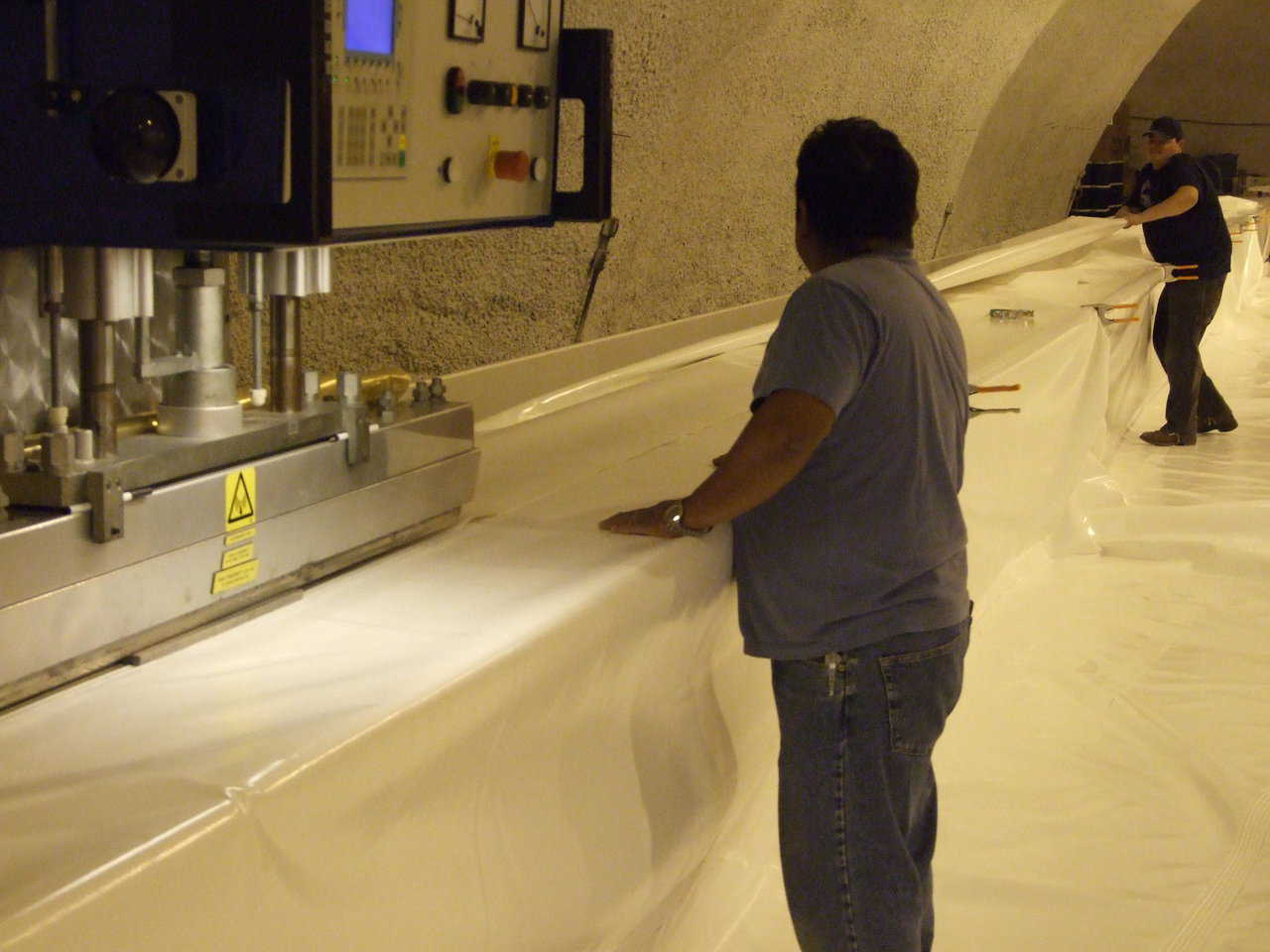
RF welder in use — The super expensive automatic machine shown runs on a track 230 feet long. It is called a radio frequency welder. It is what welds the fabric together for the Airforms. (Monolithic Staff)
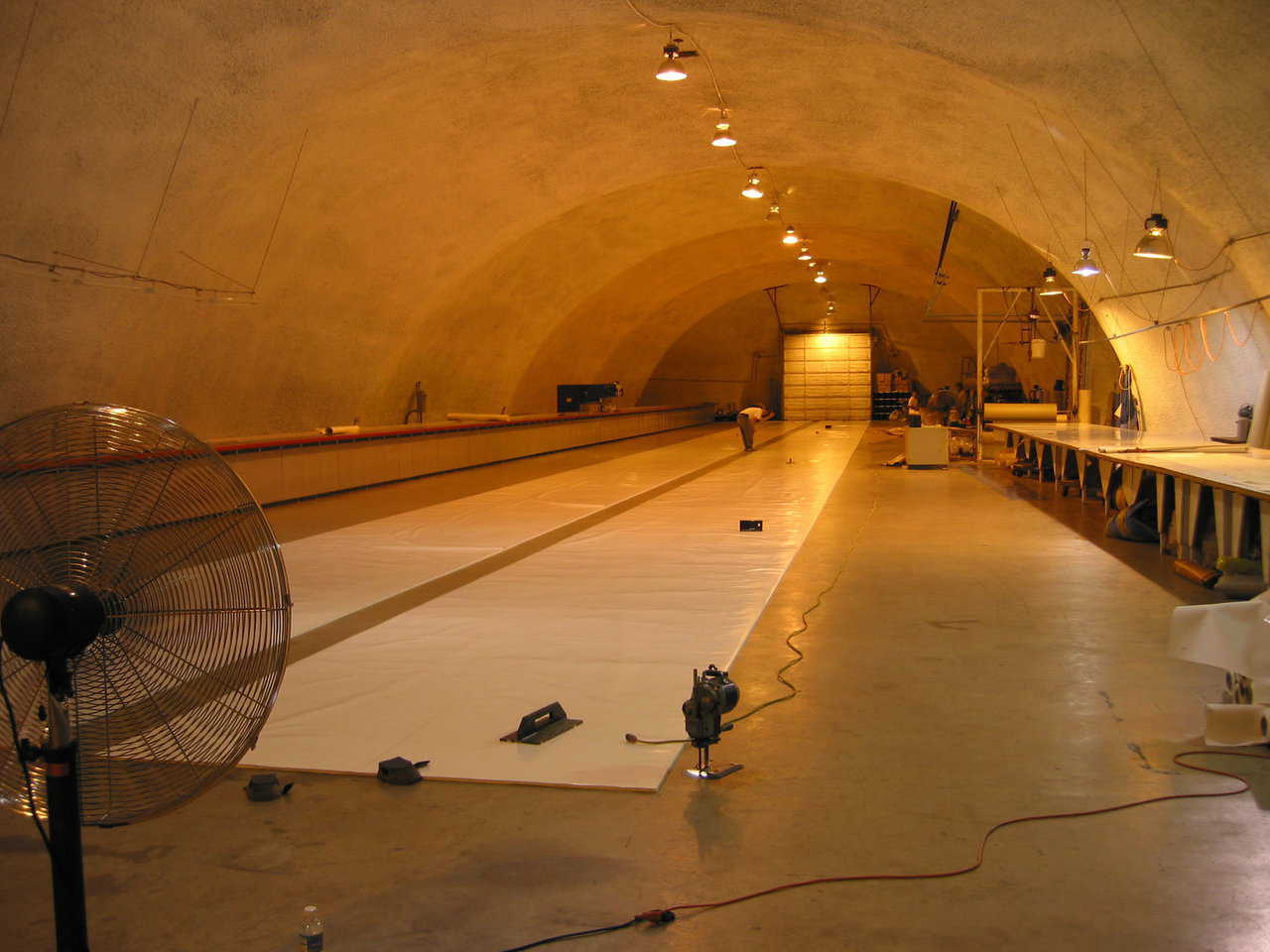
Inside Bruco’s belly — A look down the length of “Bruco” the caterpillar — manufacturing shop for the Airforms. On the floor the fabric is pulled ready for cutting another Airform. (Monolithic Staff)
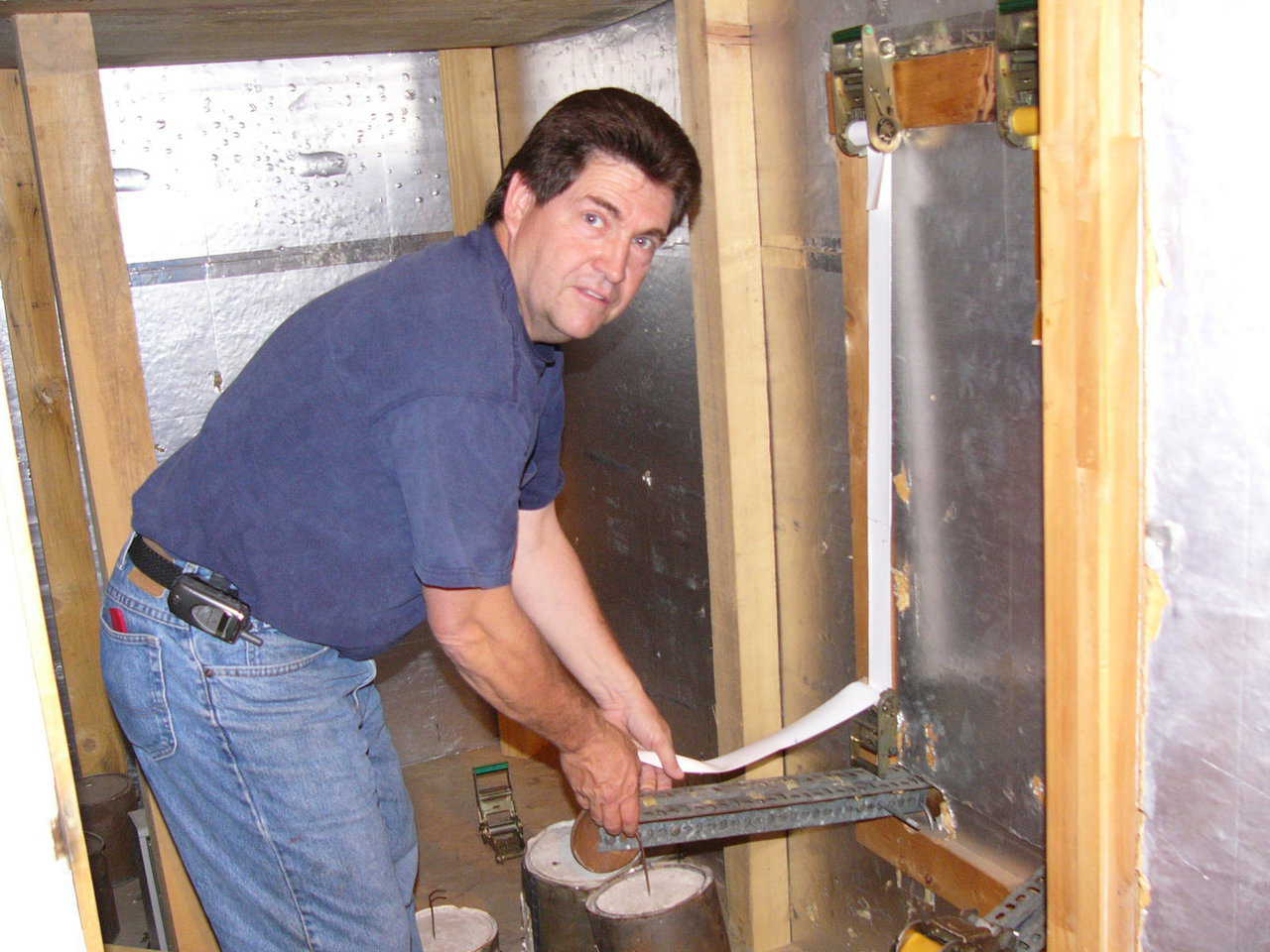
Loading fabric — Don Garrison Superintendent is loading a strip of fabric in the test blocks. Note this is done by actual weights rather than springs. (Monolithic Staff)
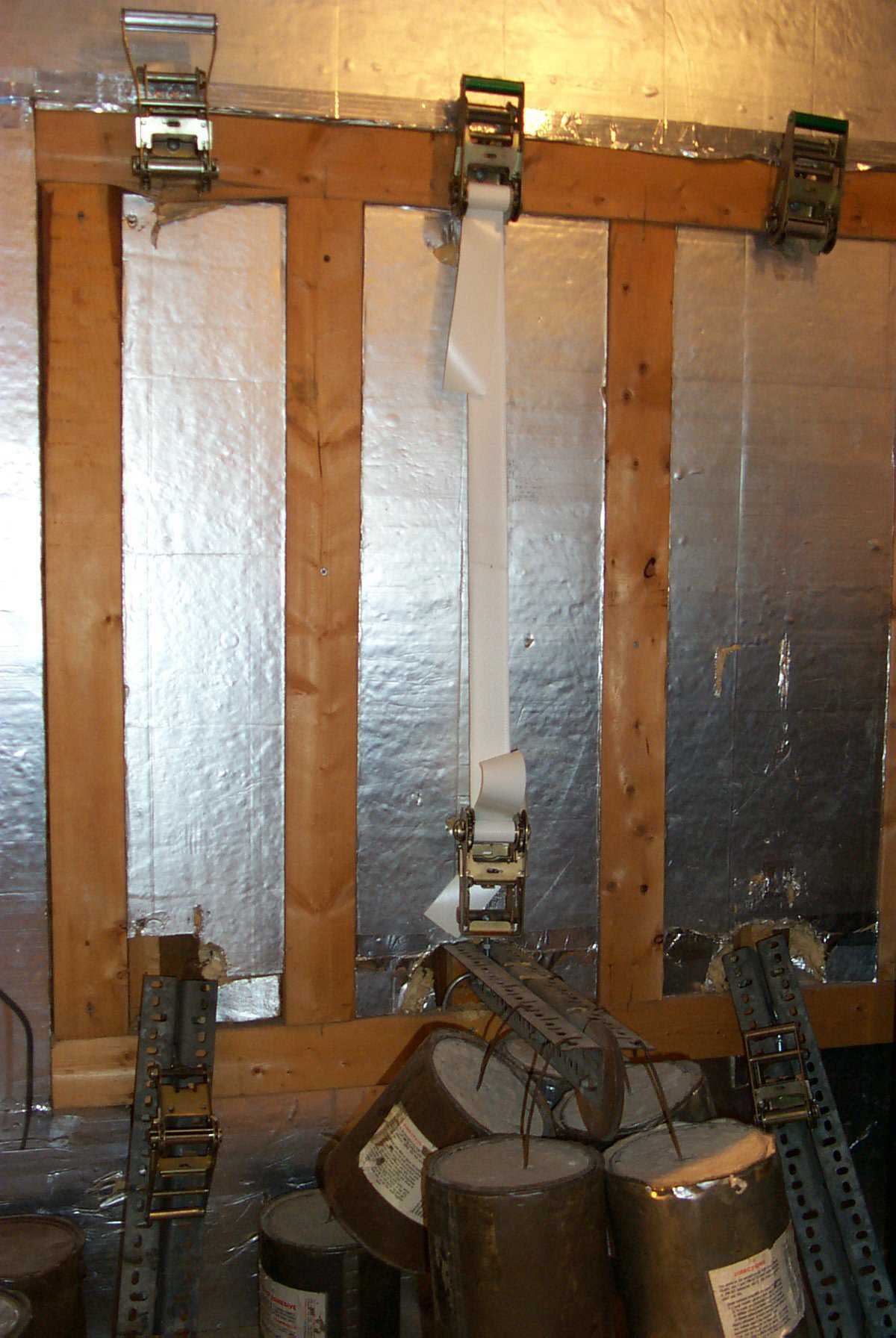
Test chamber — Inside look of the heated test chamber for testing stretch and failure of fabrics. Note the fabric is put under tension in this 140 degree F chamber for 24 hours. (Monolithic Staff)